Table of Contents
ToggleThe Importance of Kiln Drying in Wood Door Manufacturing
The importance of kiln drying in wood door manufacturing cannot be overstated. As an expert in the field of custom wood door manufacturing, I understand how crucial this process is for ensuring wood products’ quality, stability, and durability. Kiln drying involves placing timber in a controlled environment where heat, humidity, and airflow are carefully regulated to reduce moisture content, making the wood more stable and less prone to defects.
Benefits of Incorporating Kiln Drying in Wood Door Manufacturing
Incorporating kiln drying in wood door manufacturing offers numerous benefits, including:
- Enhanced Stability: Reduces risks of warping and cracking.
- Improved Durability: Ensures long-lasting wood products.
- Consistent Quality Control: Maintains structural integrity of wood doors.
This process also aligns with sustainable practices, thanks to modern kilns’ energy efficiency and resource management capabilities.
The Science Behind Kiln Drying Wood in Wood Door

Understanding Kiln Drying in Wood Door Manufacturing
As a professional in wood door production, I can vouch for the important duty that kiln drying plays in ensuring the high quality and durability of timber products. Kiln drying is a controlled process where timber is positioned in a chamber—recognized as a kiln—and based on carefully regulated heat, humidity, and airflow to minimize its moisture content. This process is vital in timber door production to attain the preferred dampness degrees that make the wood stable and durable.
The Kiln Drying Process
The kiln drying-out procedure entails several phases:
Stage | Description |
---|---|
Initial Heating | The timber is slowly warmed to raise its temperature and start the dissipation of dampness. |
Dissipation | Moisture is extracted from the timber, and the moisture inside the kiln is thoroughly managed to ensure consistent drying. |
Last Drying | The wood is brought to the target wetness content, normally between 6-8% for wood doors. |
Moisture Content Control
Managing moisture content is essential in kiln drying. Wood with high moisture levels is prone to warping, cracking, and other deformations when subjected to environmental changes. By reducing the moisture content to optimal levels, kiln drying helps preserve the structural integrity of wooden doors.
Technical Advances
Developments in kiln drying modern technology have substantially enhanced the performance and precision of the procedure. Modern kilns make use of electronic systems to keep an eye on and change temperature, moisture, and airflow in real-time. This ensures that every piece of wood is dried out evenly, decreasing problems and enhancing the general top quality of the wood doors.
Benefits of Kiln Drying in Wood Door Manufacturing
Incorporating kiln drying out in timber door-making offers several benefits:
Benefit | Description |
---|---|
Enhanced Stability | Reduces the threat of warping and cracking, guaranteeing resilient doors. |
Improved Durability | Rises resistance to ecological stressors such as moisture and temperature modifications. |
Quality Control | Ensures regular top quality and performance of the timber doors. |
Recognizing the science behind kiln drying out is important for anyone included in timber door manufacturing. It not only enhances the high quality of the final product but also adds to the efficiency and sustainability of the production process.
Benefits of Kiln Drying Over Air Drying
Rate and Efficiency
One of the key benefits of kiln drying over air drying out is the significant decrease in drying out time. While air drying out can take several months to a year, kiln drying out can attain preferred dampness levels within days to weeks. This increased procedure is particularly advantageous in wood door production, where timely manufacturing is critical to fulfill market needs.
Consistent and Controlled Environment
In a kiln, the drying environment is carefully controlled, ensuring that temperature level, moisture, and airflow are maximized for the particular timber types being dried. This level of control is not feasible with air drying, which goes through fluctuating weather. Consequently, kiln drying creates timber with more consistent dampness web content, which is crucial for the stability and performance of wood doors.
Decreased Defects
Air drying out frequently causes numerous wood issues such as bending, cracking, and unequal drying out. Nevertheless, the controlled conditions in a kiln dramatically minimize these issues. By preserving optimum drying specifications, kiln drying in timber door manufacturing reduces the threat of flaws, resulting in higher-quality output.
Improved Fungal and Insect Resistance
An additional notable advantage of kiln drying is its capacity to get rid of fungi and insects that may exist in the wood. The heat reached during the kiln drying-out process properly kills these microorganisms, enhancing the resilience and longevity of timber doors. This is a crucial aspect in ensuring the high quality and security of the final product.
Energy Efficiency
Modern kilns are designed to be energy-efficient, making use of sophisticated modern technology to decrease energy consumption while optimizing drying efficiency. Compared to the passive nature of air drying out, kilns can be extra environmentally pleasant, particularly when using sustainable energy sources. This facet of kiln drying in wood door manufacturing aligns with the expanding focus on sustainable manufacturing methods.
Area Utilization
Air drying requires significant room for stacking and saving wood over extended durations. In comparison, kilns offer an extra small and effective use area, as the drying-out process occurs in a hard setting. This advantage is particularly beneficial for wood door manufacturers with minimal space, permitting even more structured operations.
Moisture Content and Its Impact on Wood Doors
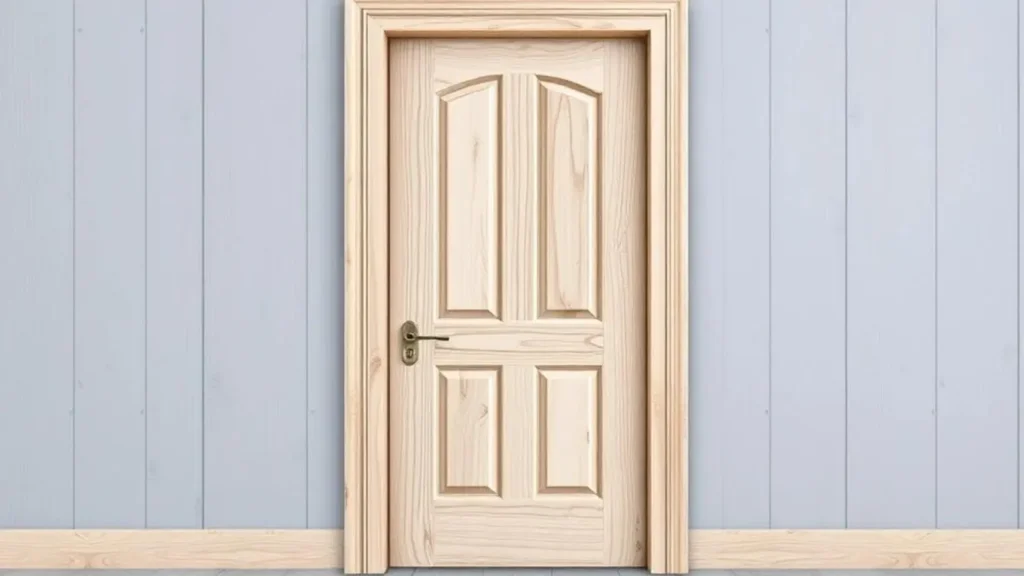
The Role of Moisture Content in Wood
Dampness material is a vital consideration in wood door production. Wood, being a hygroscopic material, absorbs and releases wetness depending on the surrounding environment. This intrinsic home necessitates a thorough understanding of how moisture web content influences timber’s physical buildings, especially in the context of door production.
Optimal Moisture Levels
For wood doors, maintaining an ideal damp web content is vital. Generally, the wood used in indoor production ought to have a wetness content of around 6-8%. This range makes sure that the timber stays steady and minimizes the probability of dimensional changes once the door is mounted.
Moisture Content (%) | Impact on Wood |
---|---|
0-5% | Wood becomes too breakable and susceptible to cracking. |
6-8% | Optimal variety for stability and longevity. |
9-12% | Wood might begin to swell and warp. |
13% and over | High risk of substantial warping, swelling, mold, and mildew growth. |
Repercussions of Improper Moisture Content
Failing to keep the appropriate dampness of web content can lead to several problems:
- Warping: Excess dampness triggers the timber to increase unevenly, bringing about bending.
- Breaking: Insufficient dampness makes the timber weak and a lot more at risk of splitting.
- Swelling: High wetness web content can cause the timber to swell, affecting the door’s fit and capability.
- Mold and mildew Growth: Excess moisture provides a reproduction ground for mold and mildew, endangering the timber’s integrity.
The Role of Kiln Drying in Wood Door Manufacturing
Kiln drying out in wood door production plays a crucial function in managing wet material. By using a controlled atmosphere, kiln drying makes certain that the wood reaches the ideal moisture degree, thus enhancing the quality and long life of the doors. The process entails thoroughly keeping an eye on and readjusting temperature and moisture levels to achieve the desired wetness content consistently throughout the wood.
Enhancing Durability and Stability in Wood Doors
Comprehending the Importance of Kiln Drying in Wood Door Manufacturing
Kiln drying out plays a crucial role in timber door manufacturing by substantially enhancing the longevity and stability of the last product. This procedure involves putting the wood in a regulated atmosphere where temperature, moisture, and airflow are carefully managed to eliminate wetness successfully. The accurate control over these aspects ensures that the wood reaches the optimal dampness web content required for producing durable and durable wood doors.
Resilience Through Moisture Reduction
One of the primary advantages of kiln drying out is the significant reduction in the wood’s moisture content. Excess dampness in timber can bring about different problems such as degeneration, fungal development, and insect infestation, all of which can jeopardize the honesty of wood doors. By decreasing the dampness content to a steady level, kiln drying out decreases these dangers, thereby boosting the toughness of the doors.
Improving Dimensional Stability
Security is another essential variable in the efficiency of timber doors. Timber is a hygroscopic material, indicating it soaks up and releases moisture based on the surrounding environment. This natural quality can trigger timber to increase and agree, resulting in warping, twisting, and various other types of dimensional instability. Kiln drying out maintains the timber by bringing it to a uniform wet material, which dramatically minimizes the probability of these problems occurring.
Regular and Predictable Performance
The regulated atmosphere of a kiln ensures that the drying-out procedure is regular and foreseeable. This consistency is important in wood door production because it leads to uniform wood homes across all doors produced. Suppliers can rely upon kiln-dried wood to behave predictably during machining, setting up, and ending up processes, leading to greater top quality and more dependable wood doors.
Enhanced Strength and Hardness
Kiln drying out enhances the timber’s stability and boosts its toughness and firmness. The removal of excess wetness enhances the density of the timber, making it extra resistant to physical damage such as dents and scrapes. This included strength is particularly helpful for timber doors, which go through constant usage and potential effects.
Long-Term Benefits
Buying kiln drying during the production process generates long-term benefits for producers and consumers. Doors made from kiln-dried timber are less likely to require repairs or replacements due to bending, breaking, or other moisture-related concerns. This longevity translates to cost savings and increased client complete satisfaction, making kiln drying a vital action in generating high-quality timber doors.
Preventing Warping and Cracking Through Kiln Drying in Wood Door Manufacturing

Comprehending Warping and Cracking in Wood Doors
Contorting and fracturing are considerable concerns in timber door manufacturing. These problems emerge mostly because of unequal wetness circulation within the wood. When the dampness material is not evenly lowered, certain areas of the wood may shrink even more than others, bringing about contractions and architectural weak points.
The Role of Kiln Drying in Mitigating These Issues
Kiln drying in timber door production plays an essential duty in stopping bending and cracking. By very carefully controlling the drying atmosphere, kiln drying out ensures a uniform reduction of moisture material throughout the wood. This procedure minimizes internal tensions that frequently bring about contortions.
How Kiln Drying in Wood Door Manufacturing Works
Throughout kiln drying, wood is placed in a controlled setting where temperature level, humidity, and airflow are meticulously controlled. This exact control allows for a steady drying-out process, which is important for maintaining the timber’s architectural stability.
Advantages of Kiln Drying in Wood Door Manufacturing
Numerous benefits of kiln drying out contribute to its efficiency in stopping bending and breaking:
Benefit | Summary |
---|---|
Attire Moisture Reduction | Guarantees even drying, reducing internal tensions and protecting against deformations. |
Controlled Environment | It permits accurate laws of temperature level, humidity, and air circulation. |
Much Shorter Drying Time | Contrasted to air drying, kiln drying out dramatically lowers the moment required to attain the preferred dampness material. |
Consistency | Offers a regular drying procedure, important for preserving the high quality of timber doors. |
Comparing Kiln Drying to Air Drying
While air drying is a conventional approach, it usually leads to uneven wetness circulation, enhancing the threat of bending and cracking. In contrast, kiln drying in timber door production offers a controlled and reliable process, making certain the timber remains secure and sturdy.
Practical Implications for Manufacturers
For manufacturers of wooden doors, spending on kiln drying procedures converts to fewer defects and higher-quality wood doors. This not only enhances the item’s long life but likewise minimizes prices related to fixings and substitutes.
Verdict
By recognizing and executing kiln drying in wood door production, suppliers can considerably lower the threats of bending and splitting, making sure the manufacturing of high-grade, sturdy wood doors.
Energy Efficiency and Environmental Benefits of Kiln Drying in Wood Door Manufacturing
Optimizing Energy Use in Kiln Drying
One of the vital benefits of kiln drying in wood door production is the ability to enhance energy use. Kilns are made to regulate temperature level, humidity, and air blood circulation specifically, which makes certain reliable drying of wood. Modern kilns are equipped with sophisticated modern technologies that monitor and readjust these criteria in real-time, decreasing energy usage while taking full advantage of drying out performance. This not only decreases functional costs but also preserves power sources.
Decrease of Carbon Footprint
By using energy-efficient kilns, producers can significantly minimize their carbon impact. Conventional air drying-out techniques often call for large open areas and prolonged periods, leading to higher power usage and better ecological impact. In contrast, kiln drying is an extra-regulated and expedited procedure, which translates to decreased power expenditure and lowered greenhouse gas emissions.
Boosted Resource Management
Kiln drying in wood door manufacturing additionally adds to better source administration. The accurate control over drying-out problems makes certain that timber is dried out consistently and to the precise moisture content required for manufacturing. This reduces waste brought on by poorly dried wood that might crack, warp, or come to be unusable. Reliable use of basic materials is not only economical but also lines up with sustainable practices by minimizing the demand for extra wood harvesting.
Usage of Renewable Energy Sources
Several contemporary kilns have been developed to include renewable resource sources, such as solar or biomass energy. This improves the environmental benefits of kiln drying. By relying upon renewable resources, producers can lower their reliance on nonrenewable fuel sources, thereby reducing their environmental effects. This shift towards lasting energy sources is a considerable action in advertising environmentally friendly manufacturing techniques.
Water Recycling and Waste Management
An additional ecological advantage of kiln drying out is the potential for water recycling and reliable waste administration. The wetness drawn out from wood throughout the drying-out process can be accumulated and treated for reuse, minimizing water waste. Additionally, the controlled atmosphere of a kiln enables far better administration of wood spin-offs, which can be repurposed or thrown away in an ecologically liable fashion.
Quality Assurance Measures in Kiln Drying in Wood Door Manufacturing Processes
Guaranteeing the highest quality in kiln drying in timber door production includes a collection of thorough control measures. These procedures are made to maintain the integrity and performance of the timber, inevitably causing remarkable timber doors. Let’s look into the crucial top-quality control actions that are integral to the kiln drying procedure.
Preliminary Moisture Content Assessment
Before the kiln drying procedure, it is essential to analyze the preliminary wetness material of the wood. This action assists in identifying the ideal drying-out routine and makes sure that the timber is dried out evenly. Exact moisture content measurement is typically done utilizing moisture meters, which offer accurate readings.
Moisture Content Level | Drying Schedule |
---|---|
High (> 30%) | Longer drying-out cycle with progressive temperature level increase |
Medium (15-30%) | Moderate drying cycle with regulated temperature |
FAQs about Kiln Drying in Wood Door Manufacturing
1. What is the role of kiln drying in wood door manufacturing?
Kiln drying plays a vital role in wood door manufacturing by reducing the moisture content of the wood to a stable level. This process prevents warping, cracking, and other issues that can compromise the quality and longevity of the doors.
2. How does kiln drying in wood door manufacturing improve the final product?
Kiln drying enhances the final product by ensuring that the wood maintains its shape and strength. Properly dried wood provides better adhesion for finishes and prevents defects, leading to a smoother, more durable door.
3. What types of wood are typically used in kiln drying for wood door manufacturing?
Common types of wood used in kiln drying for wood door manufacturing include oak, maple, cherry, and mahogany. These species are selected for their stability, workability, and aesthetic appeal.
4. What is the typical moisture content achieved through kiln drying in wood door manufacturing?
The typical moisture content achieved through kiln drying in wood door manufacturing ranges from 6% to 8%. This optimal level helps prevent dimensional changes that can occur due to varying humidity levels.
5. How long does the kiln drying process take in wood door manufacturing?
The kiln drying process in wood door manufacturing can take from several days to a few weeks, depending on the thickness of the wood and its initial moisture content. Precise control of temperature and humidity is essential during this time.
6. What are the benefits of kiln drying in wood door manufacturing?
The benefits of kiln drying in wood door manufacturing include reduced risk of warping and splitting, enhanced wood strength, and improved surface quality for finishing. This results in higher quality and more reliable doors.
7. Are there any risks associated with kiln drying in wood door manufacturing?
Yes, risks include potential over-drying, which can lead to brittleness, and the need for careful monitoring to prevent damage to the wood. However, with proper controls, these risks can be managed effectively.
8. Can kiln drying in wood door manufacturing affect the wood’s appearance?
Yes, kiln drying can affect the wood’s appearance by enhancing its color and grain patterns. Properly dried wood often exhibits a more uniform appearance, which is desirable in high-quality door manufacturing.
9. What technologies are used in kiln drying for wood door manufacturing?
Technologies such as dehumidification kilns, conventional kilns, and vacuum kilns are commonly used in kiln drying for wood door manufacturing. Each method has its advantages in terms of efficiency and quality control.
10. How does kiln drying in wood door manufacturing influence sustainability?
Kiln drying can enhance sustainability in wood door manufacturing by minimizing waste and improving the lifespan of the products. Well-dried wood uses resources more efficiently, reducing the overall environmental impact of door production.
References
- Wood Magazine, Understanding Kiln Drying, https://www.woodmagazine.com/materials-guide/lumber/understanding-kiln-drying
- Forest Products Laboratory, Kiln Drying Wood, https://www.fpl.fs.fed.us/documnts/pdf1988/kolb88a.pdf
- The Wood Database, The Importance of Drying Lumber, https://www.wood-database.com/wood-articles/drying-lumber/
- Fine Woodworking, Drying Wood: The Fundamentals, https://www.finewoodworking.com/2018/09/10/drying-wood-the-fundamentals
- Woodworkers Source, How Kiln Drying Works, https://www.woodworkerssource.com/blog/how-kiln-drying-works/
- This Old House, How to Dry Lumber, https://www.thisoldhouse.com/woodworking/21017030/how-to-dry-lumber
- The Woodshop, Why Kiln-Dried Wood is Better, https://thewoodshop.com/why-kiln-dried-wood-is-better/
- Timber Products Inspection, Wood Drying Processes, https://www.tpi-wood.com/wood-drying-processes/
- Harvard Forest, The Science of Kiln Drying, https://harvardforest.fas.harvard.edu/publications/Science-of-Kiln-Drying
- Northern Woodlands, The Benefits of Kiln Drying, https://northernwoodlands.org/articles/article/the-benefits-of-kiln-drying
- Kiln Drying Association, Kiln Drying FAQs, https://kilndrying.org/faqs
- Pennsylvania State University, Drying Wood for Woodworking, https://extension.psu.edu/drying-wood-for-woodworking
- Woodworking Network, Kiln Drying Basics, https://www.woodworkingnetwork.com/education/kiln-drying-basics
- Oregon State University, Wood Drying and Storage, https://extension.oregonstate.edu/pub/em9027
- American Wood Council, Wood Drying, https://www.awc.org/codes-standards/publications/wood-drying
- Woodworking for Mere Mortals, The Process of Kiln Drying, https://woodworkingformeremortals.com/the-process-of-kiln-drying/