Table of Contents
ToggleHollow Core Door Manufacturing Steps Guide
The steps involved in hollow core door manufacturing are a fascinating blend of precision and innovation. Every phase plays a critical role, from selecting lightweight materials to ensure cost-effectiveness, to the meticulous assembly and bonding processes. This article delves into each stage, highlighting how they contribute to creating practical and aesthetically pleasing doors.
Exploring the Journey from Raw Materials to Finished Products
In exploring the journey from raw materials to finished products, we uncover the secrets behind the popularity of hollow core doors in interior applications. These doors have become a staple in modern construction by balancing affordability with design flexibility. Join me as we navigate through the intricacies of hollow core door manufacturing, revealing the craftsmanship and strategies that ensure quality and customer satisfaction.
Introduction of Hollow Core Door Manufacturing
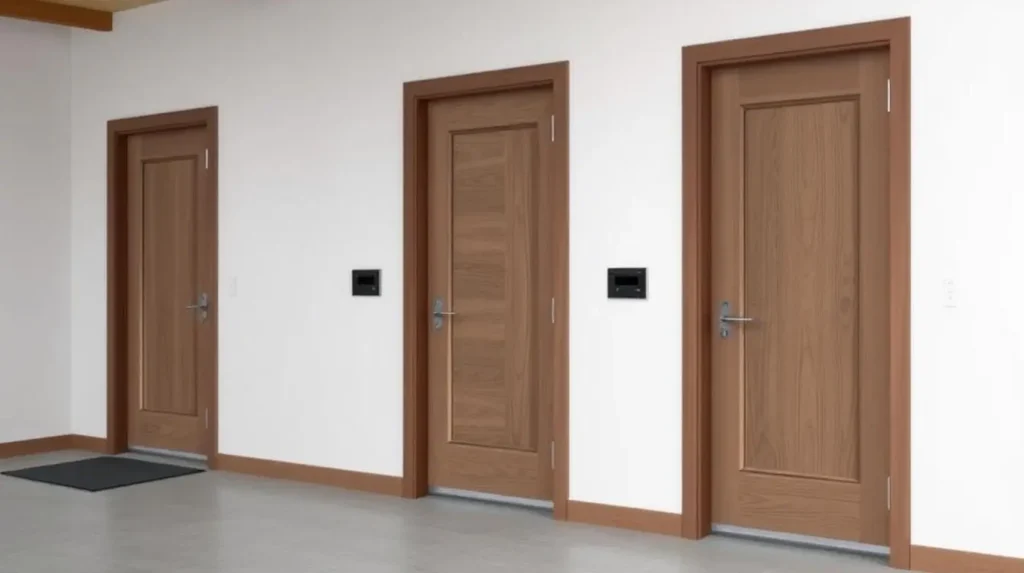
As a professional from a hollow core wood door manufacturer, I am often asked to supply a review of these special and versatile doors. Hollow core doors are a preferred option in both domestic and industrial settings because of their cost-effectiveness, lightweight nature, and simplicity of setup. They are specifically preferred for indoor applications where audio insulation and thermal effectiveness are less important contrasted to solid core doors.
What are Hollow Core Doors?
Hollow core doors are created with a lightweight core material framed within a strong outer structure, commonly constructed from timber or composite products. The core is frequently made from a honeycomb or grid-like framework, which supplies the door with its form and marginal weight while keeping architectural stability. This style not only minimizes the overall weight of the door but also significantly lowers manufacturing prices, making it an economical selection for numerous builders and property owners.
Trick Features of Hollow Core Door Manufacturing
Several key features distinguish hollow core doors from other sorts of doors:
Feature | Description |
---|---|
Lightweight Construction | Because of the products and production procedure, these doors are typically extra inexpensive than solid doors. |
Affordable | Because of the products and production procedure, these doors are typically more inexpensive than solid doors. |
Range of Designs | Available in a variety of designs and finishes to match various visual preferences. |
Ease of Installation | Their light-weight nature enables for quicker and easier installation compared to heavier alternatives. |
Common Applications
Hollow core doors are most generally used for interior applications such as:
- Bedroom doors
- Restroom doors
- Wardrobe doors
- Workplace dividings
These doors are much less ideal for exterior wood door usage because of their reduced insulation and soundproofing capacities, but they succeed in settings where convenience of usage and affordability are prioritized.
In summary, hollow core doors provide a practical option for lots of interior applications, balancing expense, weight, and style adaptability. This makes them a long-lasting option in the area of hollow core door manufacturing.
Product Selection for Hollow Core Door Manufacturing
In the hollow core door production process, selecting the ideal products is vital to ensure the end product satisfies both aesthetic and functional needs. This phase includes mindful consideration of various products that add to the door’s overall performance, resilience, and cost-effectiveness.
Core Materials
The core of a hollow core door is typically constructed using products that give architectural assistance while maintaining the door’s lightweight. Typical materials consist of honeycomb cardboard, which supplies an equilibrium between stamina and weight, and plastic or steel grids that boost longevity. The choice of core material considerably influences the door’s soundproofing and insulation residential properties.
Facings and Skins
The external layers or skins of hollow core doors are typically made from medium-density fiberboard (MDF), plywood, or hardboard. These materials are selected based on their surface area coating top quality and ability to stick to various coatings. MDF is typically favored for its smooth surface area, which is suitable for paint, while plywood is chosen for its natural wood grain appearance.
Adhesives and Bonding Agents
Effective bonding between the core and the skins is necessary for hollow core door manufacturing. The adhesives made use of should be strong sufficient to preserve the door’s integrity gradually. Commonly made use of adhesives consist of polyvinyl acetate (PVA) and urea-formaldehyde, picked for their strong bonding residential properties and resistance to environmental factors.
Edge and Frame Materials for Hollow Core Door Manufacturing
The edges and structures of hollow core doors are normally constructed from solid wood or composite products to offer added toughness and assistance. These elements are vital in keeping the door’s form and avoiding bending. The option of frame materials typically relies on the intended use of the door and the environmental problems it will certainly face.
Environmental and Regulatory Considerations
Product options have to also take into consideration environmental effects and conformity with market policies. Sustainable and environmentally friendly products are increasingly liked in hollow core door production. Makers are encouraged to pick materials that are recyclable or sourced from lasting techniques to reduce the ecological impact.
In general, the material option procedure in hollow core door manufacturing is a thorough task that requires stabilizing numerous variables to attain a product that is both practical and aesthetically pleasing.
Style and Specification Process of Hollow Core Door Manufacturing
The layout and requirements process in hollow core door manufacturing is a crucial phase that makes sure the last item fulfills both useful and aesthetic demands. This stage entails several crucial steps, each adding to the total high quality and efficiency of the door. Below, I will describe the essential components that develop this process.
Understanding Client Requirements
The initial action in the layout procedure is to understand the details needs of the customer. This entails conversations about the planned use of the doors, aesthetic choices, and any kind of specific efficiency standards such as fire resistance or soundproofing.
Style Specifications
Once the needs are outlined, the following step is to develop thorough style specifications. These consist of dimensions, core product type, surface coatings, and equipment compatibility. The requirements are recorded in a technical illustration that acts as a plan for the manufacturing process.
Material Selection
Picking the best products is crucial in making certain that the door performs as anticipated. The choice process includes reviewing numerous materials for the core, skin, and coating, based on elements such as durability, cost, and ecological impact.
Compliance with Standards
Throughout the style stage, it is critical to make certain that the door layout abides by appropriate industry requirements and guidelines. This consists of factors to consider for safety, ecological effect, and energy performance.
Model Development
Before full-scale production, a model is usually created. This permits testing and recognition of the layout, making certain that the door meets all specified demands. Any kind of required modifications can be made based on comments from this model.
Style and Specification Table
Step | Description |
---|---|
Comprehending Client Requirements | Collecting information on usage, appearances, and performance requirements. |
Style Specifications | Recording measurements, materials, and equipment needs. |
Product Selection | Reviewing and selecting proper products for core and surface. |
Compliance with Standards | Making certain design satisfies market guidelines and criteria. |
Prototype Development | Producing a prototype for testing and validation. |
Core Construction Techniques
In the realm of hollow core door production, the core building and construction stage is crucial. This stage includes creating the inner framework that supplies the door with its lightweight and cost-effective residential properties while preserving architectural integrity.
Honeycomb Core Construction
One of the most common strategies made use of in hollow core door manufacturing is the honeycomb core building and construction. This approach involves organizing a pattern of hexagonal cells made from cardboard or various other lightweight products. The honeycomb framework is renowned for its superb strength-to-weight ratio, which is essential for preserving the door’s rigidness without adding excessive weight.
Grid Core Construction
An additional widespread strategy is the grid core building. In this method, a grid pattern is produced utilizing slim wooden strips or other suitable materials. This grid serves as the framework that supports the door’s surface area layers. The grid core uses an equilibrium between stamina and weight, making it a preferred choice in hollow core door production.
Foam Core Construction
Foam core building and construction is a different technique where a lightweight foam product is made use of as the core. The foam is typically sandwiched between 2 layers of veneer or MDF (medium-density fiberboard). This approach supplies excellent insulation properties while preserving the door’s lightweight nature, which is a substantial advantage in hollow core door manufacturing.
Factors To Consider for Core Construction
When choosing a core building and construction method, several aspects have to be taken into consideration, including the intended use of the door, budget restrictions, and wanted performance characteristics. Each approach uses distinct advantages and might be preferable for details applications within the hollow core door production procedure.
Setting Up and Bonding Methods
The setting up and bonding methods in hollow core door production are important steps that guarantee the architectural integrity and performance of the final item. These procedures involve accuracy and interest in information, as they directly impact the door’s longevity and efficiency. Listed below, I will detail the essential elements of these techniques, from the preliminary setting up to the last bonding techniques.
First Assembly
In the first setting-up phase, the various parts of the hollow core door are combined. This consists of the outer framework, the core material, and any additional supports. The external framework is typically constructed from materials such as wood or steel, which provide the necessary assistance and shape for the door.
Core Placement
The core material, usually made from cardboard or various other lightweight compounds, is put within the structure. This core is crucial for preserving the door’s lightweight nature while offering some level of audio and thermal insulation. The positioning of the core should be specific to guarantee even distribution and security.
Bonding Techniques
Bonding is an important action in the hollow core door production procedure, as it guarantees that all parts are safely attached. One of the most typical bonding approaches consists of:
Bonding Technique | Summary |
---|---|
Sticky Bonding | Involves using screws, nails, or staples to secure the parts with each other. |
Mechanical Fastening | Involves using screws, nails, or staples to literally secure the parts with each other. |
Thermal Bonding | Uses heat to activate bonding agents, producing a smooth and sturdy bond. |
Precision and Quality Control
Throughout the assembly and bonding procedure, precision is critical. Each step is very carefully checked to ensure that the door meets the needed specifications and top-quality requirements. This includes monitoring for positioning, stamina of bonds, and general architectural integrity. Quality control for hollow core doors is implemented to determine and remedy any type of problems before the door carries on to the following stage of manufacturing.
By employing meticulous setting up and bonding techniques, producers guarantee that hollow core doors are both dependable and effective, satisfying the needs of different applications while maintaining cost-effectiveness.
Surface Area Finishing and Coating
In the realm of hollow core door manufacturing, surface finishing and covering play a critical duty in enhancing both the visual charm and longevity of the end product. This phase of the production procedure includes numerous precise steps, each developed to guarantee that the doors not just fulfill but go beyond industry requirements and customer assumptions.
Prep work of the Surface
The initial action in the surface area ending up is the preparation of the door’s surface area. This entails a thorough cleansing to remove any dirt, oil, or other pollutants that might have accumulated during the previous production stages. Correct surface area prep work is crucial as it makes sure that the succeeding finishings adhere effectively, preventing issues such as peeling or bubbling.
Application of Primer
Once the surface area is adequately prepared, a guide is applied. The primer works as a base coat that boosts the bond of the topcoat, supplying a consistent surface area for the final finish. It also helps to seal the pores in the material, ensuring a smooth and consistent look. In hollow core door production, selecting a suitable guide is crucial, as it can significantly affect the longevity and performance of the door.
Topcoat Application
Adhering to the guide, the overcoat is applied. This is the noticeable layer that can be personalized in regards to shade and structure to meet particular design requirements. The topcoat not only adds to the door’s aesthetic charm but also provides a layer of defense against ecological factors such as dampness, UV rays, and physical wear. Advanced application techniques, such as spray finishing, are often employed to attain a remarkable surface.
Specialized Coatings
In specific applications, added specialized layers may be related to enhancing the details residential properties of the door. These can consist of fire-retardant coverings, anti-graffiti finishes, or antimicrobial surfaces, depending upon the meant use of the hollow core doors. The selection of these layers is established by the functional requirements and the environment in which the doors will certainly be installed.
Hollow Core Door High-quality Assurance
Throughout the surface ending up and finishing process, rigorous quality assurance protocols are complied with to ensure that each door fulfills the highest possible criteria of top quality. This consists of visual inspections, attachment tests, and durability evaluations to verify that the coverings are applied properly and will perform as planned over the life of the door.
Quality Assurance and Testing Procedures
In the realm of hollow core door production, keeping rigorous quality assurance and detailed screening procedures is important to make sure that each item meets sector requirements and consumer expectations. This area outlines the critical steps and approaches used in the quality control procedure.
Inspection of Raw Materials
The quality control procedure starts with the careful inspection of resources. Guaranteeing the top quality of the products made use of in hollow core door manufacturing is vital. Common products evaluated consist of:
Material | Top quality Check |
---|---|
Timber veneers | Grain uniformity, wetness material |
Adhesives | Bonding toughness, thickness |
Core materials | Thickness, uniformity |
In-Process Quality Checks
Throughout the production process, in-process high-quality checks are performed to guarantee that each stage of production complies with established standards. Secret checkpoints include:
- Core building: Ensuring the core is equally dispersed and devoid of flaws.
- Setting up: Verifying that bonding approaches are correctly used and elements are securely secured.
- Surface ending up: Checking for harmony in finishes and finishes.
Final Product Testing
Upon conclusion of the production process, each hollow core door goes through a series of final tests to confirm its efficiency and resilience. These examinations usually include:
Test | Objective |
---|---|
Load screening | Review the door’s capability to endure pressure |
Effect resistance | Review door’s capability to endure pressure |
Sound insulation | Procedure acoustic efficiency |
Documentation and Traceability
Keeping detailed documentation is a crucial component of quality assurance in hollow core door production. This includes records of material assessments, in-process checks, and last testing results. Such paperwork ensures traceability and liability throughout the production cycle.
Continuous Improvement
Quality assurance is not a fixed procedure. It entails continuous improvement approaches, where comments from testing and customer experiences are used to refine manufacturing procedures and improve item high quality. This dedication to renovation guarantees that hollow core doors remain trustworthy and high-performing.
Packaging and Distribution Strategies
In the realm of hollow core door production, efficient product packaging and circulation strategies are vital to make certain that the end product gets to customers in a pristine problem. These approaches encompass several vital factors to consider, from the selection of packaging products to the logistics of transport and distribution.
Packaging Materials and Techniques
One of the primary concerns in product packaging is the selection of materials that supply sufficient protection during transportation. For hollow core doors, this frequently entails making use of a mix of safety covers and inflexible materials to guard against damage. Common materials consist of:
Material | Function |
---|---|
Corrugated Cardboard | Gives architectural support and padding. |
Foam Padding | Takes in shocks and protects against surface scrapes. |
Plastic Wrap | Offers a moisture obstacle and keeps parts intact. |
These materials are frequently incorporated in layers to make certain thorough protection. Additionally, the packaging procedure might involve custom-fit layouts that adjust to the specific measurements of the hollow core doors, minimizing movement within the plan.
Classifying and Documentation
Precise labeling and documentation are necessary aspects of the packaging procedure. Each plan needs to consist of clear tags suggesting the contents, dealing with instructions, and location details. This makes sure that the doors are managed appropriately during transit and get to the proper area.
Transportation and Logistics
Efficient transportation is an additional vital component in the circulation technique. The option of transport setting—whether by vehicle, rail, or sea—relies on aspects such as distance, expense, and delivery timelines. It is vital to collaborate with trustworthy logistics partners that recognize the nuances of carrying building materials like hollow core doors.
To maximize logistics, producers often use strategies such as:
Strategy | Advantage |
---|---|
Course Optimization | Minimizes transit time and gas prices. |
Stock Management | Guarantees prompt accessibility of products for delivery. |
Just-In-Time Delivery | Lessens storage space demands at the destination. |
Guaranteeing Customer Satisfaction
The supreme goal of product packaging and distribution approaches in hollow core door manufacturing is to ensure client contentment. This involves not just supplying products promptly but also ensuring they get here in excellent condition. By executing extensive high-quality checks at every phase of the product packaging and circulation process, makers can maintain their reputation for dependability and quality.
In conclusion, the actions associated with product packaging and dispersing hollow core doors are as important as any type of other phase in the manufacturing procedure. By concentrating on safe product packaging, reliable logistics, and clear communication, producers can effectively supply top-notch items to their customers.
FAQs on Hollow Core Door Manufacturing
1. What materials are typically used in hollow core door manufacturing?
- Hollow core door manufacturing usually involves materials like wood or MDF for the outer frame and honeycomb cardboard or foam for the inner core. The surface is often finished with a veneer or paint-grade MDF.
2. What is the process of hollow core door manufacturing?
- The process of hollow core door manufacturing includes building the frame, inserting the core material, attaching the face panels, pressing, trimming, and finishing steps like sanding, priming, or painting.
3. Why is cardboard honeycomb used in hollow core door manufacturing?
- Cardboard honeycomb is used in hollow core door manufacturing because it provides a strong, lightweight structure, which helps keep the door light and affordable while maintaining stability.
4. What are the standard dimensions produced in hollow core door manufacturing?
- In hollow core door manufacturing, common dimensions include heights of 80 inches and widths ranging from 24 to 36 inches, with a typical thickness of 1 3/8 inches for interior doors.
5. How does hollow core door manufacturing affect door durability?
- Hollow core door manufacturing generally results in doors that are lighter and less durable than solid core doors. While suitable for standard interior use, they are less resistant to damage from impact.
6. How does hollow core door manufacturing impact soundproofing capabilities?
- Due to their hollow core, doors produced by hollow core door manufacturing provide limited soundproofing compared to solid core doors. The lightweight core does not block sound as effectively as denser materials.
7. What types of finishes are commonly applied in hollow core door manufacturing?
- In hollow core door manufacturing, finishes include wood veneers, laminates, or paint-grade MDF, providing options for both painted and natural wood finishes depending on the desired aesthetic.
8. How does hollow core door manufacturing reduce production costs?
- Hollow core door manufacturing reduces production costs by using less raw material and lightweight core materials, making the doors cheaper to produce, handle, and ship compared to solid core doors.
9. What advancements have been made in hollow core door manufacturing?
- Recent advancements in hollow core door manufacturing include improved adhesives and lightweight core materials that enhance door strength, as well as more sustainable materials to reduce environmental impact.
10. How does hollow core door manufacturing address environmental concerns?
- Hollow core door manufacturing can be more sustainable by using recycled materials for the core, reducing the need for solid wood, and lowering shipping energy due to lighter weight, making it an environmentally friendly option.
References
- TheHomeSapiens, “Hollow Core Doors: Key Considerations Before You Purchase,” https://thehomesapiens.com/hollow-core-doors-key-considerations-before-you-purchase
- RemodelOrMove, “What Are Hollow Core Doors? Pros, Cons & Buying Guide,” https://www.remodelormove.com/what-are-hollow-core-doors
- The Carpenter’s Shop, “Types of Door Cores: Hollow Core and Solid Core Explained,” https://www.thecarpentersshop.net/types-of-door-cores-hollow-core-and-solid-core
- Home Improvement Tactics, “The Basics of Hollow Core Door Manufacturing,” https://www.homeimprovementtactics.com/basics-hollow-core-door-manufacturing
- DoorTech, “Interior Door Options: Hollow Core, Solid Core, and Polycore Doors,” https://www.doortech.co.nz/interiordoors-mojave
- Quality Door & Hardware, “Hollow Core Doors vs. Solid Core: Pros and Cons,” https://www.qualitydoor.com/blog/hollow-core-vs-solid-core
- Homenish, “Guide to Hollow Core Doors: Construction and Uses,” https://www.homenish.com/guide-to-hollow-core-doors
- RBA Door, “What Are the Different Types of Interior Doors?” https://www.rba.co.uk/blog/interior-door-types-guide
- Architecture Lab, “Door Types Explained: Solid vs. Hollow Core,” https://www.architecturelab.net/solid-vs-hollow-core-doors-explained
- DoorNMore, “How Are Hollow Core Doors Manufactured?” https://www.doornmore.com/hollow-core-door-manufacturing-guide
- Doors and Beyond, “Interior Doors: Hollow Core or Solid Core?” https://www.doorsandbeyond.com/blog/hollow-core-doors-benefits-and-drawbacks
- Bob Vila, “Cost-Effective Options: Hollow Core Door Manufacturing,” https://www.bobvila.com/hollow-core-doors-costs-guide
- HomeGuide, “The Pros and Cons of Hollow Core Doors,” https://www.homeguide.com/hollow-core-doors-pros-and-cons
- This Old House, “Choosing the Right Interior Door: Hollow Core vs. Solid,” https://www.thisoldhouse.com/interior-door-selection-guide
- EnergyStar, “Energy Efficiency in Hollow Core Doors,” https://www.energystar.com/hollow-core-doors-efficiency-tips
- Fine Homebuilding, “Durability Factors in Hollow Core Doors,” https://www.finehomebuilding.com/hollow-core-door-durability-guide